高真空减压蒸馏作为一种有效的分离纯化技术,在有机化学、石油化工、生物制药等多个领域中广泛应用。然而,在实际操作过程中,特别是在处理对热敏感的目标产物时,如何有效避免其在高温蒸馏过程中的热分解风险,成为了科研工作者和工程师们关注的重要课题。本文将探讨高真空减压蒸馏条件下降低目标产物热分解风险的方法。
首先,优化蒸馏温度是关键。在高真空环境下,物质的沸点显著降低,因此可以通过调控系统内的真空度来适当降低蒸馏温度,从而减少目标产物因高温而发生热分解的可能性。同时,精确控制升温速度与恒温时间,避免温度骤变导致的局部过热现象,也是防止热分解的有效手段。
其次,采用适当的保护剂或稳定剂。对于某些易于热分解的化合物,可以在蒸馏前加入适量的稳定剂或者通过共蒸馏的方式引入一种能与其形成稳定复合物的物质,以降低目标产物在蒸馏过程中的活性,达到抑制热分解的目的。
再者,改进蒸馏装置及工艺流程设计。例如,使用内壁涂有惰性材料(如特氟龙)的蒸馏器,可降低目标产物与设备表面的反应活性;采用分段蒸馏或回流冷凝相结合的技术,既能提高分离效率,又能避免目标产物长时间处于高温状态。
此外,智能监控与自动化控制技术的应用也不容忽视。实时监测蒸馏过程中的压力、温度以及物料变化,并利用先进的PID控制器进行精准调节,确保整个蒸馏过程始终在安全、稳定的范围内运行,有助于较大限度地降低目标产物的热分解风险。
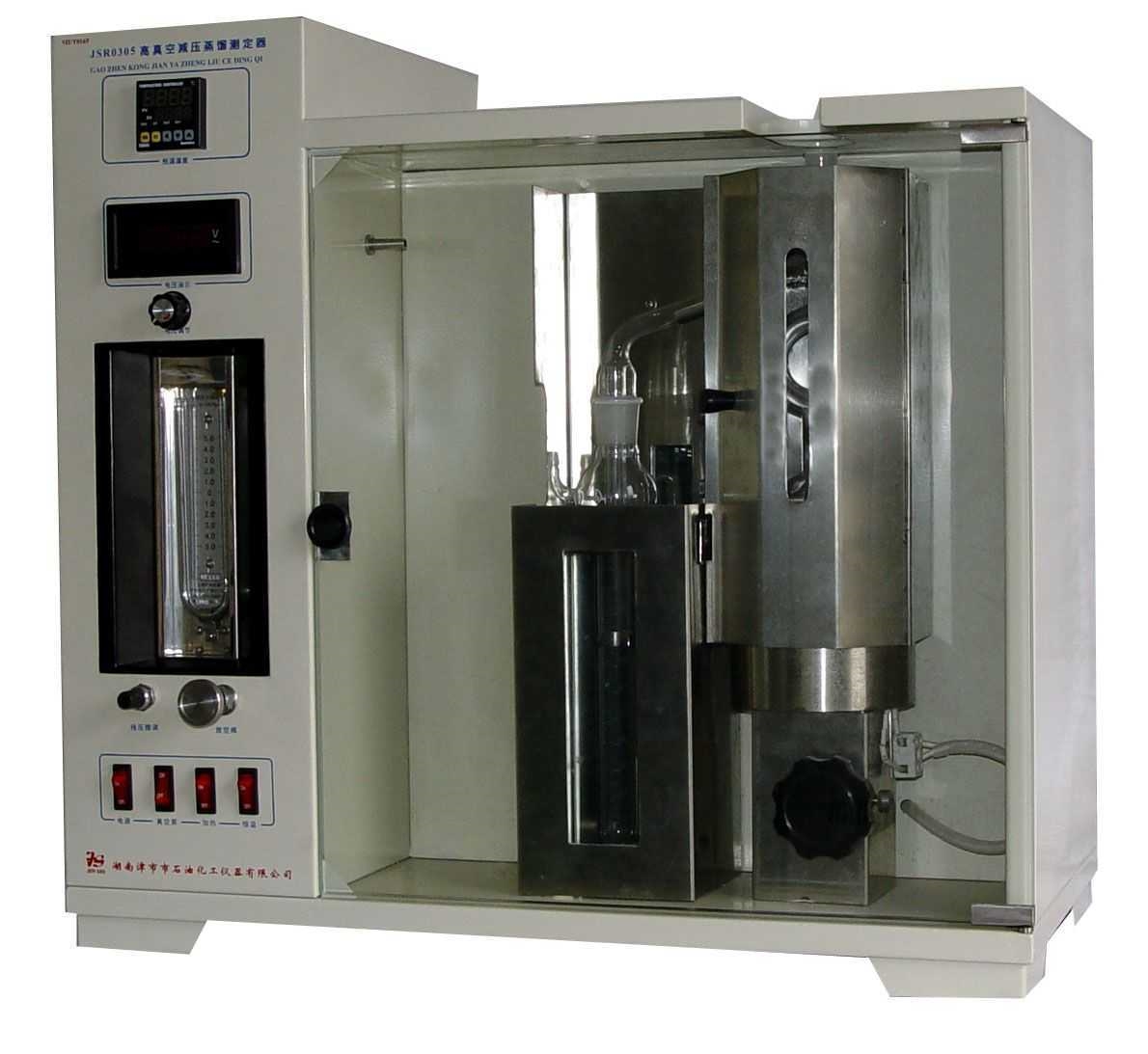
而且,实验室研究和工业生产中还需结合具体目标产物的性质,不断摸索并验证新的保护策略和技术方法,包括新型冷却技术的研发、微波辅助蒸馏技术的应用等,以期在保证高真空减压蒸馏效果的同时,有效防范目标产物的热分解问题,实现更高效、更安全的分离纯化过程。